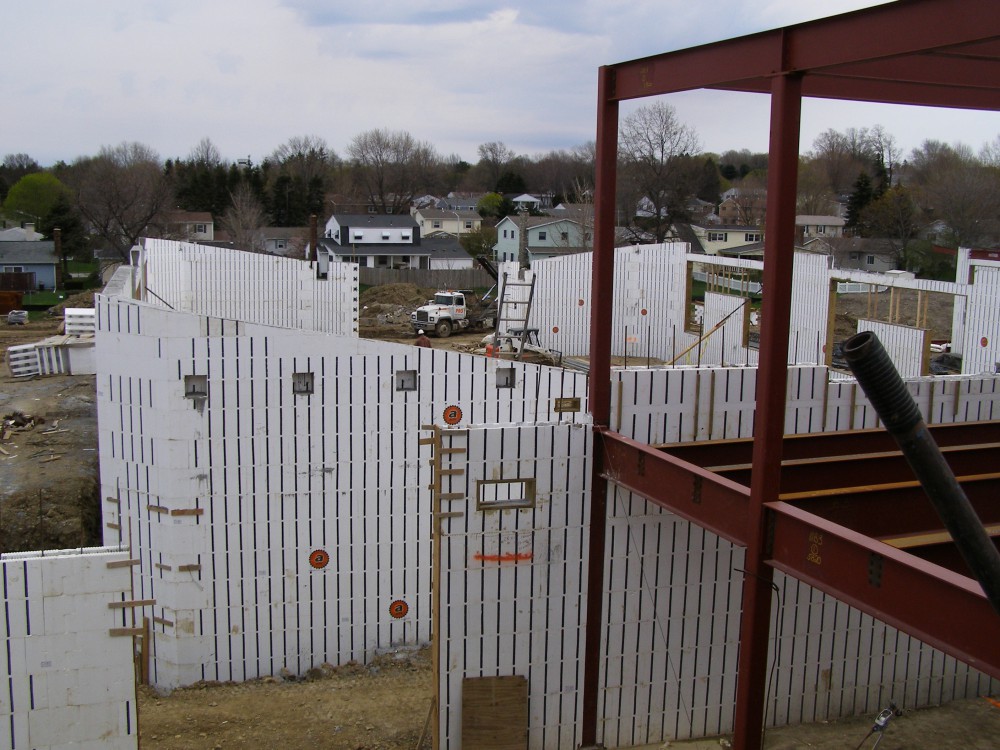
Insulated Concrete Forms vs. Conventional Wood Framing
The construction of buildings using insulated concrete forms (ICFs) offers numerous tangible benefits over wood-frame construction, including energy savings, durability, the speed of construction, reduced environmental impact and insurance savings. Also, ICF walls are effective vapor barriers, and they suppress the transmission of sound as well.
There are also intangible benefits to consider, like increased peace-of-mind for property owners, tenant satisfaction and a greater perception of value by prospective buyers.
ICF BENEFITS VS. WOOD FRAMING
Here are some of the areas where ICF construction offers key benefits over its wood-frame counterpart.
ENERGY SAVINGS
High-performance ICF buildings save energy from cradle to grave. A 2017 study quantifies energy savings possible with ICF construction. Energy savings accrue because 1) concrete’s thermal mass reduces temperature swings, and 2) high R-value rigid foam insulation on either side of the wall further minimizes heating and cooling loads.
According to ICF Builder, a 2017 study by UL’s CLEB Laboratories quantified this thermal mass effect. It conducted tests in accordance with ASTM C1363-11, comparing standard 6-in core ICF construction (with 2.5-in thick Type II EPS foam on both the exterior and interior), and traditional R-20 2×6 stud construction with interior drywall and exterior vinyl siding. Researchers calculated that ICF construction reduced energy use by 58 percent.
DURABILITY
Compared to conventional wood framing, concrete walls better withstand the most dramatic assaults that structures endure in Pennsylvania, including tornadoes, hurricanes, floods and fires. ICF walls have been tested in some of the most difficult real-world conditions, including a 2013 F5 tornado that struck south of Oklahoma City, OK.
ICF walls also provide superior resistance to insects, including termites. In general, concrete’s durability increases lifespans as it decreases life-cycle costs, particularly for maintenance and repairs.
QUICK AND SIMPLE
ICF forms can be assembled by a modest number of workers. Once the forms are in place, concrete pouring is typically completed in a matter of hours. Since concrete is contained within layers of rigid foam insulation, curing can continue while other aspects of the project proceed.
ENVIRONMENTAL IMPACT
According to the ICFA, during the approximate 75-year life cycle of an ICF structure, about 85 percent of the positive environmental impact of ICFs comes from reduced heating and cooling costs, while the other 15 percent “is traced to material production, transport and demolition.”
When it comes to production, concrete mixes can include fly ash and/or recycled concrete aggregates. The rigid insulating panels can be connected by spacers fashioned from recycled polypropylene. Any steel reinforcement can be fabricated from material that is mostly recycled. The minimal waste generated during construction is 100 percent recyclable.
Overall, ICFs use fewer natural resources than traditional wood-frame construction.
INSURANCE SAVINGS
Fire containment capabilities of ICF construction are superior, and any fire risk from electrical wiring within the wall is dramatically reduced. Strong concrete walls stand up to natural disasters. Thanks to ICF’s storm and fire resistance, owners often enjoy reduced insurance premiums throughout the lifespan of the structure.
CASE STUDY: WINDOM HILL PLACE
Pittsburgh’s Windom Hill Place is a luxury townhome development that embodies common ICF advantages. ICF construction was also an ideal structural response to the challenging hillside topography.
Insulated concrete forms were a key element in a highly sustainable design that also included:
- EnergyStar-rated HVAC system
- Energy recovery ventilation system
- Bamboo and cork floors
- Low-VOC finishes
- Plentiful natural lighting to reduce use of artificial lighting
- Lower level exterior cast stone cladding including recycled content
- Upper-level exterior metal cladding featured recycled metal
Setting up the four-foot-long ICF wall sections only required 5-6 workers, and it only took six hours to fill the forms with a standard concrete mix. The building was erected in just two weeks.
Since the rear of the building is built into a steep slope, ICF rear walls for the lower two levels there included 10 inches of concrete between 2.5-inch layers of exterior and interior rigid insulation. The 320 cubic yards of concrete for the project used fly ash to make it a more sustainable product.
The 2,800 square feet of living area in each unit features clear-span construction that offers a buyer tremendous freedom of design. Structural concrete supports a fourth-level balcony capable of holding a hot tub, trees or gardens.
Finally, the embrace of ICF construction helped brand Windom Hill Place as a high-quality development deserving of higher valuations.
EFFECTIVE LCA USAGE
A life cycle assessment (LCA) quantifies environmental impacts over a project’s entire lifecycle by noting costs associated with every phase from pre-construction through demolition. It provides essential information to those planning a new building construction project, and it often helps a project accumulate more LEED points.
MIT’s Concrete Sustainability Hub (CSHub) notes common issues with LCAs. Sometimes, LCAs get too cumbersome and costly, and they may appear too late in the process to sufficiently impact design.
CSHub has studied ways to make LCAs more integral to the design process to maximize their impact. Hub researchers speak of the “chasm” between the findings of LCA research and the utilization of those findings by developers, architects and builders. A CSHub Webinar, “Buildings: Life Cycle Assessment,” identifies a need to:
- Better assess complete life cycles
- Take a more holistic approach
- Better incorporate LCAs into the design process
The CSHub team developed a streamlined approach to LCAs that requires lesser amounts of data and time while cutting costs and reducing uncertainty. This should promote assessments earlier in the design process where they’ll have the greatest impact.
ABOUT PACA
The Pennsylvania Aggregates and Concrete Association (PACA) provides technical, educational and promotional information that serves members dedicated to professionally building and connecting communities throughout Pennsylvania.
In an era of sustainability, ICFs are gaining favor among all stakeholders in commercial and multi-family projects. Please reach out to us for more information about the advantages of ICF construction.